South American and European experts demonstrated how to turn agro- and forestry residues into high value products
The ValBio-3D project – Valorization of residual biomass for advanced 3D materials – developed efficient technologies for production of sustainable and 100% biobased materials from agro-industrial residues, addressing the bioeconomy of the future, and based on cost-efficient production of biochemicals, bioplastics, biocomposites and tailor-made nanocelluloses. The ValBio-3D project was a three-year project (2017-2019) and counted with the collaboration of 3 European and 3 South American R&D groups, in addition to the involvement of relevant industry.
“This project has corroborated our hypotheses, that industrial agro- and forestry waste can be valued, in particular, sugarcane bagasse and pine sawdust, transforming them into high-value products such as wound dressings or sustainable biocomposites. This avoids the need to deposit or burn this waste, also providing economic gains”
Dr. Maria Cristina Area (IMAM, Argentina)
coordinator of the project
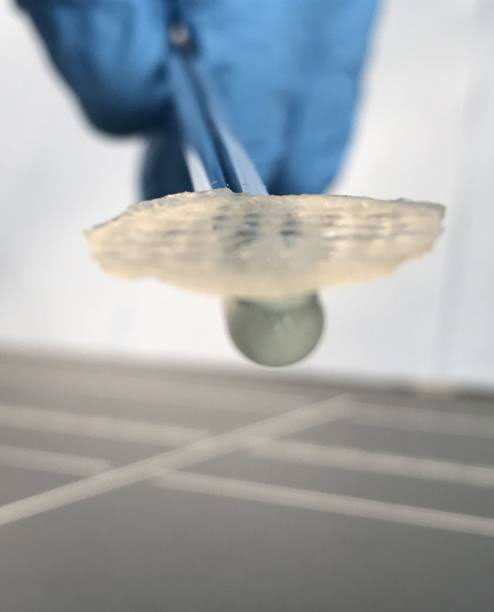
3D printed construct composed of TEMPO oxidized bagasse nanocellulose and alginate. (Photo: Gary Chinga Carrasco, RISE PFI).
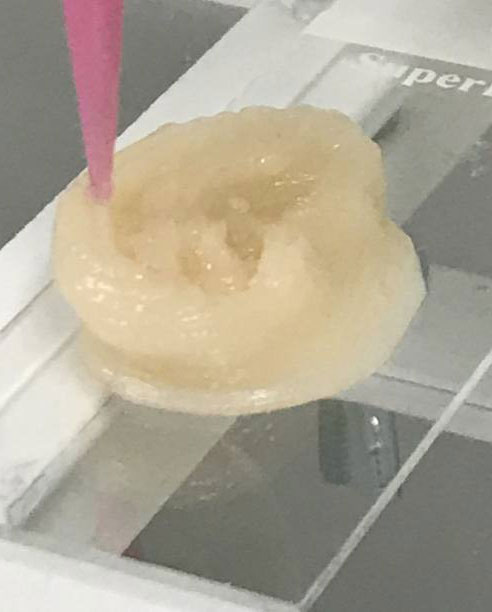
3D printed self-standing ear model using high consistency nanocellulose from pine residues. (Photo: Gary Chinga Carrasco, RISE PFI).
The multidisciplinary scientists joined forces to perform the demanding activities that were planned for the project period, “it is not easy to convert an agro-industrial residue into a high-value product, especially if we focus on biomedical applications”, adds Dr. Gary Chinga Carrasco (RISE PFI, Norway). “Fortunately, we counted with the extensive competence of IMAM when it comes to pulping and fractionation, our RISE PFI competence about tailor-made nanocelluloses and biocomposites for biomedical applications, and also involved the expertise from RISE Bioscience when it was necessary to test the potential of the materials for wound dressing devices”, complements the experienced scientist.
Some of the main activities regarding valorization of residual biomass included nanocellulose and biocomposite production, and 3D printing. Various nanocelluloses were obtained and tested, including materials with varying composition and that were chemically or enzymatically pre-treated. “In our case, one of the main project results was the advancement of the high consistency enzymatic fibrillation (HefCel) technology towards new raw materials (pine sawdust pulp, bagasse), cytotoxicity tests of the enzymatically fibrillated cellulose materials and 3D printing trials of the cellulose hydrogels”, mentions Dr. Heli Kangas (VTT, Finland).
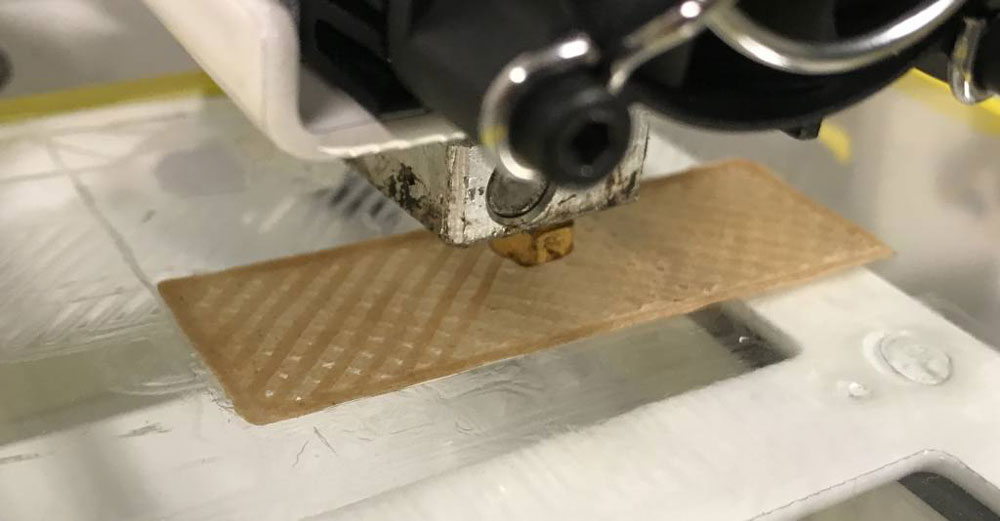
3D printing of a biocomposite structure by fused deposition modeling (FDM) technology. The biocomposite is composed of biocompatibilizers and biobased polyethylene from sugarcane, and sugarcane bagasse fibers obtained in the project (Photo: Gary Chinga Carrasco, RISE PFI).
Another route explored by the research group was the production of bioplastic, which is expected to be biosourced, sustainable and renewable. “This also required an optimal fractionation, simultaneous saccharification and fermentation to improve the yield for second generation bioplastic production, that is from residual wastes”, adds Dr. Area. Bioplastic production is more expensive that conventional fossil plastics, however, the scientists demonstrated that the combination of bioplastic with lignocellulosic fibres from, for example, bagasse could be beneficial. Such biocomposites could be made with a lower economical cost and improve the environmental performance, compared to neat plastics or bioplastics. “These results are very interesting from an industrial and environmental perspective and we are working extensively to finish some papers that describe the advancements in this direction, especially considering the life cycle assessment of the biocomposite materials”, describe scientists Diana Ita Nagy and Isabel Quispe (PUCP, Peru).